What if your drinking cup could tell you its best-by date?
A UK-based startup has developed world’s first biodegradable solution that leaves no microplastic behind and decomposes plastic
The idea is unique and you may think of it as unachievable. How can a plastic cup tell you by when you should use it? Think about it, we buy plastic cups, particularly for gatherings and parties, but never bother to check how long that chunk of plastic has been in that state. Once you’re done using plastic cups, they pollute the garbage dumps and eventually end up in rivers or seas. Plastic, by its property, does not degrade.
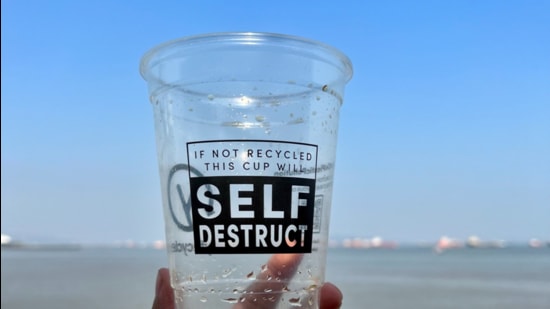
A UK-based startup Polymateria has developed world’s first biodegradable solution that leaves no microplastic behind and decomposes plastic into a wax-like structure that is nature-friendly. The product is called Lyfecycle.
At the Great Future Showcase organized by the UK government, HT spoke with Niall Dunne, CEO of Polymateria, about the technology that makes plastics biodegradable over a period of time, the importance of India as a research hub and why it isn’t any more expensive to make these cups compared with regular plastic cups.
Polymateria was founded in 2015. They had announced earlier this summer that they’ll be working with Indian companies including Godrej for wider use of fully degradable plastic in packing applications. The company has also developed a proprietary additive that is added, in pellet form, into the plastic resin during the manufacturing process. The industrial category for this additive is called masterbatch and it contains catalysts and cocatalysts which remain dormant for a specified period, mentioned on the plastic products as the expiry date or best-by date or recycle-by. They then begin to break down the hard crystalline and amorphous structure of plastic into a wax-like form. Here are the edited excerpts of the interview.
What is this unique technology that makes plastics different from plastics we have known so far?
We’ve created a new technology which is self-destructing plastic. What’s unique about it is that it’s time contrived, so we can program it - when the plastic is being made and its exact usefulness, so that’s a date by which the technology becomes active, and it starts the process of return to nature. That’s really useful because it allows you to communicate clearly to consumers that you want them to use it, you want them to reuse it, maybe recycle it and you can build in enough time for all of those things to happen. You program that in when you make it and once the time is off, if it’s in the natural environment as 32% of all plastic is (that’s about 4 billion tonnes), it will return to nature. We’ve managed to get it falling back to nature in 336 days without microplastic and without harming the environment. So that’s unique because previously technologies were fracturing plastic which was not fully biodegradable.
What is the Living Lab that Polymateria has made?
We’ve launched new standards, we’ve pushed out a lot of peer-reviewed documentation and there’s a ton of science that sits behind this as you’d imagine coming from Imperial College, London. But the reason we’re doing this is to create ‘seeing-is-believing’ moments. Particularly young people, they don’t really want to read lots of technical information, they just want to know if something works. One of the ways we’re engaging them is by showing them the two key features of the technology by experiences.
This Living Lab is a way we show what the product looks like and how people use it and enjoy it, and then we put it in there. Because we know that it can biodegrade in 336 days, we’ll film that. There’s one going to go to Chennai and it’s going to be managed by independent scientists who will record everything that happens. We’ve done one in Dakar and we’re going to do one in Brazil later this year. This is how we bring science to life on the biodegradation side. On the recycling side, we then show people that if they do the right thing, we can collect some of these cups and upcycle them and turn them into cool products like bracelets.
What is the chemical aspect of this technology? How are you changing the composition of plastic and are you adding or removing something from it?
We’re really doing three fundamental things. The time-controlled aspect is something we design at the point of manufacturing, and we can do it in the resin. We are working with a company called Formosa. With them, we have developed the ability to build it in the resin so when the resin is being made, we can design the three fundamental characteristics that make the plastic different in the resin or we can do what’s called the masterbatch stage.
Masterbatch is an additive. Now historically, additives haven’t worked because they haven’t had enough understanding of the material itself, and they haven’t been sophisticated enough to destroy the crystalline region, which is a big reason why they’ve created microplastic and haven’t been successful. So, time controls piece, technically what’s happening there, it is a combination of catalysts and cocatalysts that acts sacrificially for a period of time.
We’ve given enough catalyst and cocatalyst for this to act for two years. Once they’re exasperated and depleted, nothing is stopping the two other things from happening. We added the ability to destroy the hard crystalline region, as well as the amorphous region of the polymer structure. You’ve got oligomers to make polymers, you need to go to two monomers and then polymers, what we’ve done is we’ve basically reverse-engineered the polymer back into an oligomeric stage. To us, that’s grease or wax.
How costly is it to manufacture these plastic cups? Are there recurring costs?
Typically, these cups are about 10 to 15% more expensive than traditional plastic. If you’re charging a penny for the plastic, it will be a rounding error you won’t even notice it if you’re a consumer. We want to incentivize volumes. In terms of the recurring costs, there’s no additional capital expenditure. Probably the only real recurring cost would be the stewardship of the technology and making sure it’s getting used and deployed in the right way.
Is India an important research hub for this tech?
We’ve been working with Clarient (now called Avient after the merger with Poly One) in India for several years. They are now the world’s largest performance chemicals company and they’ve been in India since 1967. They have been our kind of technical partners throughout the last couple of years. And it’s quite exciting because what it offers is an end-to-end solution. A kind of a true Made in India scenario, so the ability to manufacture here, prototype here as well as develop and test in India. We are testing at eight different facilities in India from Chennai to CIPET, the Central Institute of Petrochemicals Engineering & Technology of the government of India.